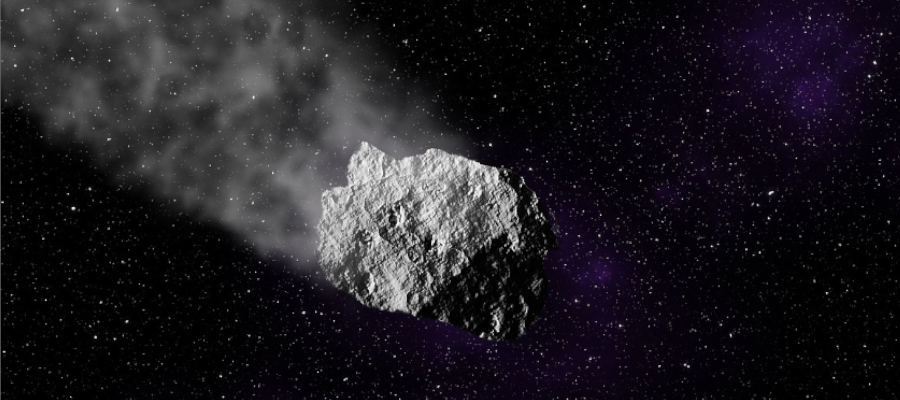
Analyse par éléments finis d'un composant FPA 2k² avec ANSYS MAPDL pour le programme européen ASTEROID
Les principaux objectifs d'ASTEROID sont de développer des matières premières de très grande taille compatibles avec la fabrication de détecteurs de très grande taille en volume tout en conservant le même niveau de performance. Afin d'améliorer la stabilité thermo-mécanique du FPA de 2k², l'optimisation de la structure du FPA et du flux de processus sera faite par la modélisation thermo-mécanique par ADDL. L'objectif principal d'ADDL dans le programme ASTEROID est de développer une méthodologie pour simuler le flux de processus pour un Focal Plane Array de 2k² en utilisant des simulations d'éléments finis avec ANSYS MAPDL. Les résultats seront utilisés par LYNRED pour optimiser le processus d'assemblage. Les fichiers d'entrée des calculs doivent inclure la possibilité de changer l'épaisseur, la taille, les données des matériaux, les conditions limites et les charges pendant le projet.
En considérant les dimensions de l'ensemble du paquet et le nombre de boules pour la couche d'interconnexion, certaines hypothèses ont été prises en compte pour construire le modèle de paquet FPA. Le maillage d'un assemblage qui comprend un réseau de billes de 2088 x 2088 où chaque bosse de soudure est explicitement modélisée conduira à un modèle avec plus de 4 millions d'éléments solides. Les capacités informatiques actuelles ne permettent pas de modéliser explicitement toutes les billes d'indium d'un BGA (Ball Grid Array) complet. Pour réduire la taille du modèle d'éléments finis et le garder raisonnable, ADDL a développé une méthodologie basée sur les règles d'homogénéisation utilisées pour les matériaux composites afin de remplacer la couche d'interconnexion par un matériau équivalent homogène (HEM). L'objectif principal de cette approche est de reproduire la rigidité de la couche d'interconnexion avec le HEM. La validation du HEM est faite en comparant les résultats d'un calcul thermo-mécanique entre 2 modèles FE à différentes températures. Le premier est un assemblage avec un vrai BGA 20 x 20, l'autre est un assemblage avec HEM.
Déplacement (µm) dans la direction Z dans le modèle 20x20 à la température de polymérisation
L'objectif étant de réduire la flexion de la couche de substrat pendant le processus d'assemblage, les fichiers d'entrée des calculs doivent permettre de modifier l'épaisseur, la taille, les données sur les matériaux, les conditions limites et les charges. Les scripts APDL sont bien adaptés pour prendre en compte tout changement dans le modèle FE. Pour réduire la taille du modèle d'éléments finis et le garder raisonnable, des considérations symétriques ont été prises en compte. Un modèle à symétrie d'un quart a été analysé pour ce projet.
Modèle d'éléments finis à symétrie ¼ pour le composant complet du réseau plan focal
Pas d'amincissement Déplacement Uz - (mm)
Le processus d'assemblage thermique a été décomposé en étapes de chargement (températures, conditions aux limites, assemblage des pièces, etc...) qui correspondent aux étapes des calculs à effectuer (Load Step).
Les résultats de post-traitement des calculs donnent une tendance sur le comportement de l'ensemble du paquet pendant l'assemblage du flux de processus. En ce qui concerne les spécifications du projet, des calculs ont été effectués pour étudier l'effet de différents facteurs. Les résultats de post-traitement suivants donnent un exemple des données et des capacités fournies par les calculs. Les résultats présentés ici sont extraits de l'analyse de l'épaisseur de la couche de substrat du projet ASTEROID.
Étape d'amincissement Contrainte de Von-Mises - (MPa)
Article rédigé par Julien BARNERIAS (Ingénieur d'Études chez ADDL)